The quality control plan is a fundamental document that defines the procedures, methods and standards necessary to ensure that the products or services comply with the established quality requirements. Its main purpose is to identify and prevent errors or non-conformities before they impact on the customer, thus optimising the production process and reducing costs.
QUALITY CONTROL PLAN: TIPS TO EXCELLENCE
by marketing on 5 de December de 2024
QUALITY ASSURANCE PLAN: A GUIDE TO SUCCESSFUL IMPLEMENTATION
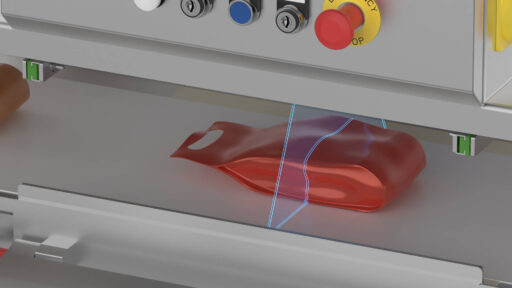
BENEFITS OF IMPLEMENTING A QUALITY CONTROL PLAN
Having a well-structured quality control plan brings multiple advantages to the company, positively impacting all levels of the production process.
The main benefits are detailed below:
The main benefits are detailed below:

Improving operational efficiency
The implementation of a quality control plan allows errors to be detected and corrected early in the process. By establishing preventive controls, workflows are optimised, production time is reduced and more efficient processes are achieved. This results in cost savings and a more effective use of human and material resources.

Ensuring customer satisfaction
Effective quality control ensures that products consistently meet the standards expected by customers. This not only improves brand perception and loyalty, but also reduces the likelihood of complaints, generating greater trust in the company and its brands. Customer satisfaction is fundamental to any business, and the quality plan helps to achieve this.

Compliance with regulations and standards
The quality control plan facilitates compliance with legal regulations and industry standards, which are essential to operate in many sectors. For example, in the food or pharmaceutical industry, product quality and safety are regulated by strict standards, and a quality plan helps to meet these requirements. In addition, regulatory compliance protects the company from legal sanctions and strengthens its position in the market.
Implementing a quality control plan not only improves the company's internal processes, but also optimises the use of resources and ensures regulatory compliance, resulting in a significant competitive advantage.
HOW TO MAKE A QUALITY CONTROL PLAN
A quality control plan requires a systematic and detailed approach to ensure that each stage of the production process meets established standards. Below are the key steps in developing an effective plan and how Varpe teams contribute to this process:

Define Project Objectives and Requirements
This step involves identifying the specific quality objectives and regulatory requirements applicable to the product. It is essential to establish what is expected from the control plan in order to be able to measure its effectiveness.

Identify Products and Services to Control
Determine which critical processes require more rigorous quality control. Identifying critical points ensures that resources are focused on areas of greatest impact.

Selecting Control Tools and Methods
Define what tools and methods will be used to measure and control quality. This includes visual inspections, laboratory tests, internal audits and other methods.
Varpe as a leading provider of quality control solutions, provide advanced dynamic weighing and contaminant detection technologies. These tools are especially valuable in sectors such as food and pharmaceuticals, where quality standards are critical. Varpe's equipment, such as industrial weighing systems, allows continuous weight monitoring and contaminant detection, ensuring that each product meets the required specifications without stopping the production flow.
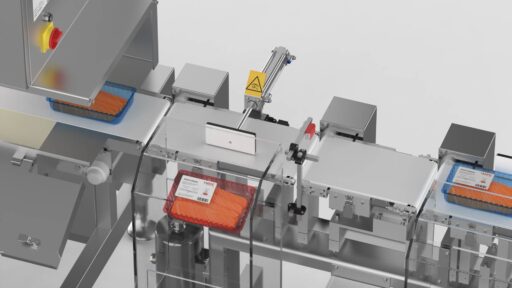

Assign Responsibilities and Roles
Clearly defining roles and responsibilities within the quality team is crucial to ensure that each task is covered. This facilitates follow-up and ensures that everyone is committed to the plan.

Establish a Calendar of Activities
Draw up a timetable detailing the control actions, their periodicity and deadlines. This schedule allows for better organisation and control of the planned activities.

Develop a Corrective Action Plan
Define a set of corrective actions to address any deviations or non-conformities that may arise in the quality control process. This helps to minimise the impact of problems and allows for rapid correction.

Review and Validate the Plan
Finally, it is important to conduct a thorough evaluation of the plan. Periodic review ensures that the control plan is kept up to date and adapted to changes.
Varpe's support in the development and execution of a quality control plan is key for industries that require accuracy and consistency in their products. Varpe's dynamic weighing and contaminant detection solutions contribute to the effective implementation and maintenance of quality standards at every stage of the production process.