The Kaizen method, which translates from Japanese as ‘continuous improvement’, is a management philosophy that has transformed numerous industries around the world. This strategy is not only applicable to manufacturing and production; it can also revolutionise the efficiency and effectiveness of industrial weighing systems. Below, we will explore how you can apply the Kaizen method to optimise weighing systems in your company.
Kaizen method: What is it and how can you
implement it in industrial weighing systems?
by marketing on 10 de June de 2024
KAIZEN METHOD: WHAT IS IT AND HOW CAN YOU IMPLEMENT IT IN INDUSTRIAL WEIGHING SYSTEMS?
UNDERSTANDING THE KAIZEN METHOD
The Kaizen method originated in Japan after World War II, mainly in the automotive industry, as an approach to continuously improve processes and eliminate waste. This philosophy involves small, constant improvements involving all levels of an organisation. Its implementation not only improves operational efficiency, but also promotes an inclusive and collaborative work environment.
In the context of industrial weighing systems, Kaizen can be a valuable tool to ensure accuracy, reduce downtime and improve the quality of the final product.
In the context of industrial weighing systems, Kaizen can be a valuable tool to ensure accuracy, reduce downtime and improve the quality of the final product.
BENEFITS OF THE KAIZEN METHOD IN INDUSTRIAL WEIGHING SYSTEMS

IMPROVED ACCURACY
In industrial weighing systems, accuracy is critical. Small continuous improvements in calibration and maintenance processes can significantly reduce measurement errors, which is vital to ensure compliance with quality and regulatory standards.

REDUCTION OF DOWNTIME
Implementing Kaizen can help identify and eliminate the causes of unexpected downtime or delays in weighing systems. By optimising maintenance routines and improving operational efficiency, downtime is minimised, resulting in increased productivity..

INCREASED CUSTOMER SATISFACTION
Weighing accuracy can directly affect customer satisfaction, especially in industries where products are sold by weight. Constant improvements in weighing systems ensure that customers receive exactly what they expect, which can improve brand perception and customer loyalty.
IMPLEMENTING THE KAIZEN METHOD IN YOUR INDUSTRIAL WEIGHING SYSTEMS
MANAGEMENT COMMITMENT
The first step in implementing kaizen in industrial weighing systems is management commitment. Leaders must understand and support the importance of continuous improvements in weighing processes and allocate resources to train personnel and adjust processes as needed.
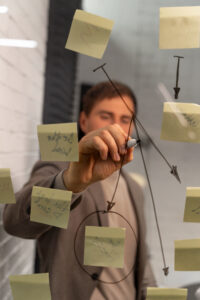
TRAINING AND AWARENESS RAISING
All employees must understand how they can contribute to the improvement of weighing systems. Training should range from basic kaizen principles to specific techniques for maintaining and calibrating weighing equipment.
To this end, training should range from the basic principles of the Kaizen method, such as identifying "muda" (waste), to advanced techniques specific to maintaining and calibrating weighing equipment efficiently. It is also essential to teach how small errors or oversights in weighing can have a major impact on accuracy and thus brand perception.
In addition, employees should be encouraged to think proactively about how they can improve their work areas. This may include suggestions on how to make calibration procedures more efficient, or ideas for reducing human error during weighing. To facilitate this involvement, many companies have implemented reward systems that recognize and reward significant contributions to process improvement.
To this end, training should range from the basic principles of the Kaizen method, such as identifying "muda" (waste), to advanced techniques specific to maintaining and calibrating weighing equipment efficiently. It is also essential to teach how small errors or oversights in weighing can have a major impact on accuracy and thus brand perception.
In addition, employees should be encouraged to think proactively about how they can improve their work areas. This may include suggestions on how to make calibration procedures more efficient, or ideas for reducing human error during weighing. To facilitate this involvement, many companies have implemented reward systems that recognize and reward significant contributions to process improvement.
OPEN COMMUNICATION CULTURE
Creating an environment where workers feel comfortable sharing their ideas and suggestions is crucial. This can include regular brainstorming sessions or a suggestion system that allows employees to propose improvements directly.
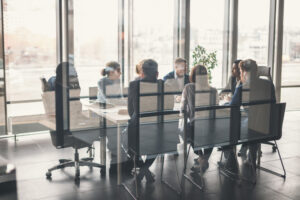
SMALL IMPROVEMENTS AND FOLLOW-UP
The implementation of the Kaizen method in industrial weighing systems focuses on making small, continuous improvements and meticulously monitoring their effects. This incremental approach allows companies to adjust their processes in a systematic and sustainable way, maximising accuracy and efficiency without destabilising existing operations.
Starting with small changes can include adjustments such as periodic recalibration of weighing equipment to ensure accuracy or reorganisation of workspace to improve the flow of operations. These improvements, while they may seem minor, have the potential to generate significant long-term benefits.
Starting with small changes can include adjustments such as periodic recalibration of weighing equipment to ensure accuracy or reorganisation of workspace to improve the flow of operations. These improvements, while they may seem minor, have the potential to generate significant long-term benefits.
It is crucial that each change implemented is accompanied by a rigorous monitoring process. This involves establishing specific key performance indicators (KPIs) to help measure the effectiveness of each improvement. For example, in the case of weighing systems, metrics such as the decrease in variability of recorded weights or the reduction in the number of machine stoppages due to weighing errors could be monitored.
In addition, continuous monitoring can quickly identify any adjustments that are not working as expected, making it easier to make informed decisions on whether to continue, modify or stop implementations. This test and evaluation cycle is essential to the spirit of continuous improvement promoted by the Kaizen method and ensures that industrial weighing systems not only maintain their accuracy and efficiency, but also evolve with the changing needs of the company and its customers.
In short, the Kaizen method offers a robust framework for continuously improving industrial weighing systems. By adopting this philosophy, you can not only optimize the accuracy and efficiency of your operations, but also strengthen organizational culture and improve customer satisfaction. Are you ready to start implementing these improvements in your company?